When it comes to workplace safety, understanding the difference between risk assessment and hazard identification is crucial. These two concepts might seem similar, but they serve distinct purposes in creating a safer environment. By recognising their unique roles, you can ensure your safety strategies are both effective and comprehensive.
Hazard identification focuses on spotting potential dangers that could cause harm. It’s about identifying what could go wrong. Risk assessment, on the other hand, goes a step further by evaluating the likelihood and impact of those hazards. Together, they form the foundation of proactive safety management.
By distinguishing between these processes, you’ll not only comply with regulations but also protect your team and resources. Knowing when and how to apply each can transform your approach to safety, making it more efficient and reliable. So, let’s explore how these two essential practices work hand in hand to minimise risks.
Understanding Risk Assessment And Hazard Identification
Risk assessment and hazard identification are both critical for managing workplace safety. They address different aspects of potential dangers but work together to reduce harm.
Definitions And Key Differences
Hazard identification focuses on spotting potential sources of harm. Examples include exposed wiring, heavy machinery, or toxic substances. It’s about recognising threats before they cause issues.
Risk assessment examines the likelihood and severity of harm from these hazards. For instance, a properly shielded machine presents a lower risk compared to one with exposed parts. This process prioritises actions based on the level of danger.
Importance In Safety Management
These processes form the foundation of effective safety management. Identifying hazards ensures you’re not overlooking threats, while assessing risks helps allocate resources to the most pressing issues.
Regulatory compliance relies on both steps. For example, health and safety legislation in NZ, such as the Health and Safety at Work Act 2015, mandates systematic hazard and risk evaluations to protect employees.
Components Of Risk Assessment
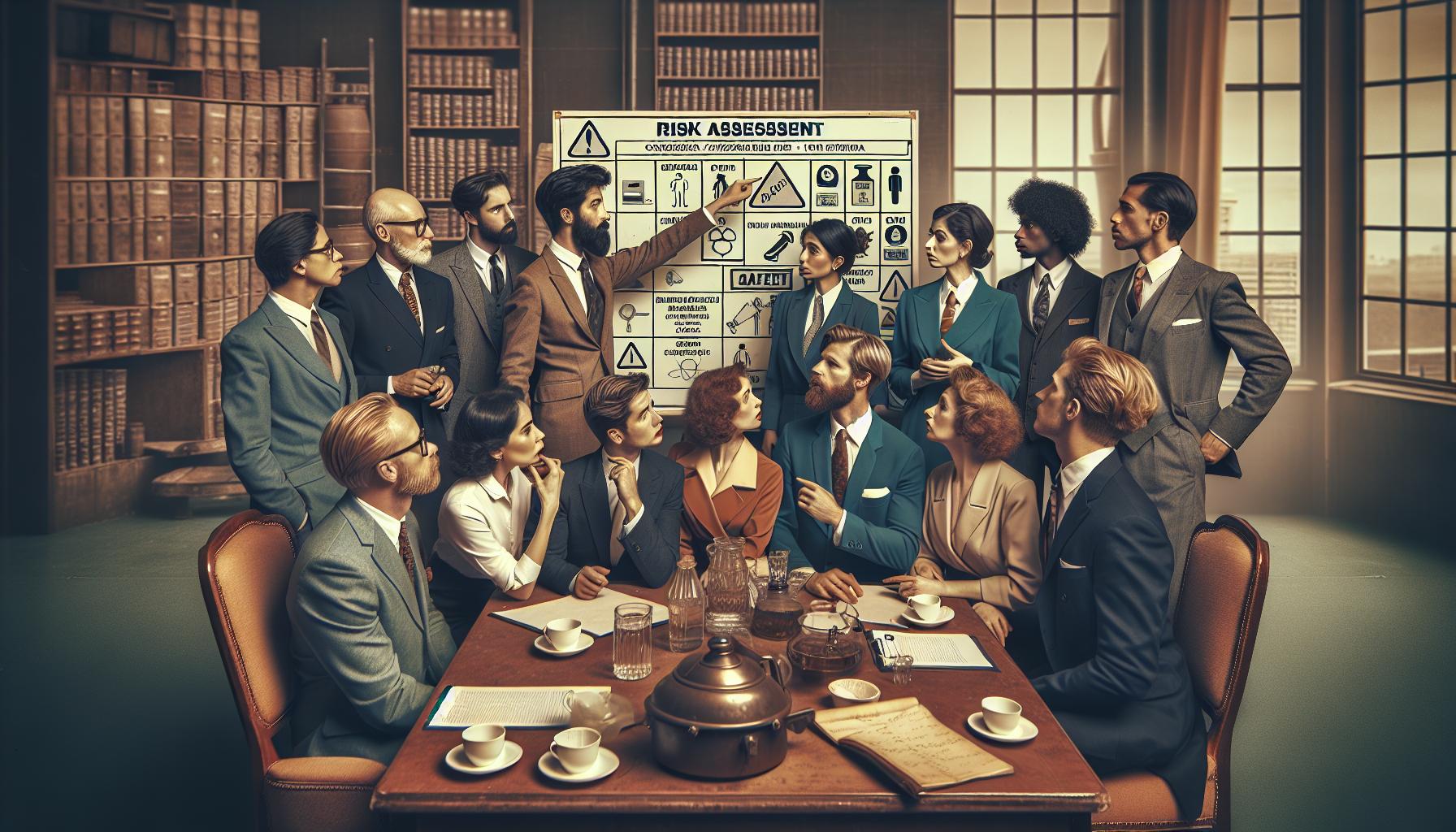
Risk assessment breaks down into multiple stages to help identify potential issues and create effective strategies to manage them. These components ensure hazards are evaluated systematically.
Risk Analysis
Risk analysis involves examining identified hazards to understand their potential consequences and likelihood of occurrence. This process includes gathering data, assessing exposure levels, and considering factors like the work environment or employee interaction with hazards. For example, you might analyse how working near flammable materials could lead to fire incidents under specific conditions.
Risk Evaluation
Risk evaluation compares the findings from the analysis against established safety standards or organisational criteria. It identifies which risks need immediate action and helps prioritise controls. If your workplace uses the HSE’s risk matrix guidance, you could determine whether risks fall into low, medium, or high categories, guiding decisions on resource allocation effectively.
Elements Of Hazard Identification
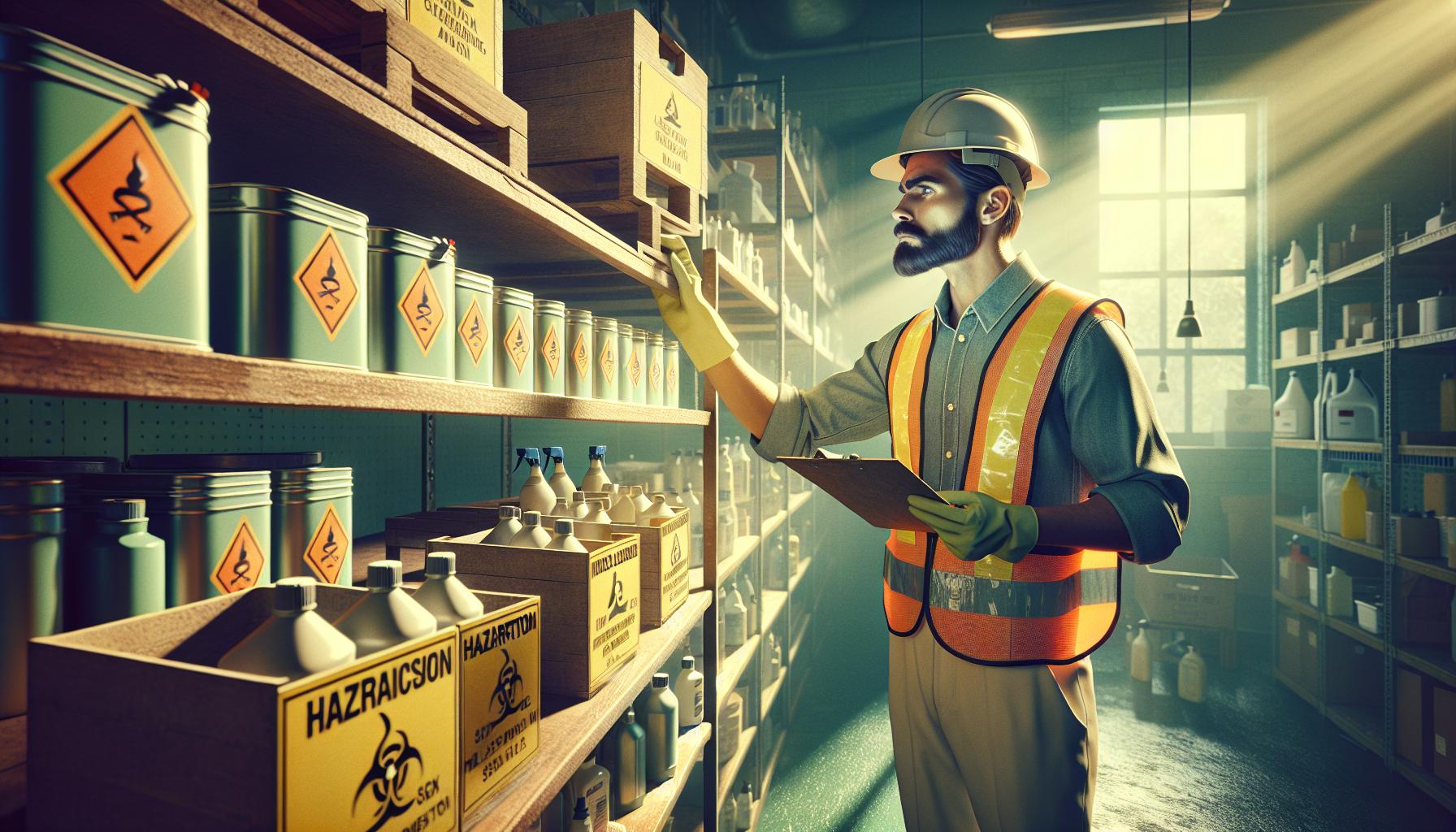
Hazard identification serves as the critical first step in managing workplace risks. By focusing on recognising potential dangers, you can proactively work to create a safer environment.
Identifying Potential Hazards
You identify potential hazards by closely examining every aspect of the workspace. Common hazards include physical objects like unstable shelving, chemical risks like cleaning agents, biological dangers such as mould, or ergonomic issues like repetitive strain. Use observations, employee feedback, and inspection records to spot these risks.
Assessing Hazard Severity
You assess hazard severity by determining how much harm the identified dangers could cause. Focus on factors like the number of people exposed, possible injuries, and the conditions under which hazards could emerge. High-severity dangers often involve serious injury or long-term health effects, while low-severity hazards might lead to minor harm like small cuts or discomfort. Quantifying severity ensures practical prioritisation in safety measures.
Comparing Risk Assessment Vs Hazard Identification
Both risk assessment and hazard identification are crucial for workplace safety, but they serve different purposes. Understanding their distinctions helps you apply them effectively.
Process Differences
Hazard identification comes first and focuses on spotting potential dangers. You examine the environment to identify risks like slippery floors, exposed wires, or heavy equipment. It’s about recognising what could cause harm.
Risk assessment follows hazard identification. It goes beyond listing hazards, evaluating how likely those threats are to cause harm and the severity of possible outcomes. This process includes analysis and assigning levels of risk—low, medium, or high—based on the likelihood and impact.
Applications In Various Industries
Different industries rely on hazard identification and risk assessment in unique ways. In construction, you identify dangers like falling objects, unstable scaffolding, or heavy machinery risks, then assess their impact on site safety. In healthcare, hazard identification might focus on exposure to biohazards, while risk assessment ensures safety protocols are adequate for managing infections.
Manufacturing prioritises machine-related hazards, with risk assessments addressing operational risks like equipment malfunctions. In education, you might identify hazards such as blocked fire exits or unsafe playground equipment and assess how they affect staff and students. These processes adapt to industry-specific challenges to maintain safety effectively.
Benefits Of Combining Both Approaches
Combining hazard identification with risk assessment supports a thorough approach to workplace safety. Using both methods together ensures you’re addressing hazards effectively and prioritising actions based on their impact.
Improved Decision-Making
Assessing hazards alone offers incomplete insights, while combining both approaches sharpens decision-making. Hazard identification highlights potential dangers, and the subsequent risk assessment evaluates their significance. This layered process ensures your resources are allocated where they’re most needed, reducing the chance of underestimating high-risk hazards. For example, spotting unstable equipment (hazard) before assessing its likelihood of causing harm (risk) allows clear prioritisation. Eventually, this refined evaluation prevents oversights and enhances clarity in safety strategies.
Enhanced Workplace Safety
Merging the strengths of both methods creates a safer work environment by addressing risks systematically. A holistic safety approach ensures you’re not only finding hazards but also measuring their impact and implementing control measures effectively. For example, identifying ergonomic risks like poor workstation setup and assessing their long-term effects can reduce strain-related injuries. Combining these practices leads to targeted interventions, sustained safety improvements, and greater compliance with safety standards like the Health and Safety at Work Act 2015.
Challenges And Limitations
Risk assessment and hazard identification, though essential, have their own set of challenges. These can arise from resource constraints, procedural misunderstandings, and human errors, among other factors.
Overcoming Common Barriers
Limited resources often make it difficult to carry out thorough assessments. Tight budgets or understaffed teams may lead to incomplete evaluations, which can compromise safety. For instance, not prioritising regular inspections due to time constraints can cause hazards to go unnoticed.
Inconsistent data collection hampers accurate hazard identification and risk evaluation. If assessments depend on unorganised or outdated information, the results may not reflect real-world conditions. Maintaining up-to-date records and a structured process is vital for reliable assessments.
Resistance to change or lack of involvement from employees slows down the implementation of safety measures. Without team buy-in, addressing hazards and risks effectively becomes an uphill task.
Addressing Misconceptions
Confusion between hazard identification and risk assessment results in insufficient safety practices. Some assume spotting hazards equals managing risks, but without assessing likelihood and impact, dangers remain poorly addressed.
Believing that these processes are optional creates compliance and safety issues. Underestimating their significance often leads to regulatory breaches. For example, neglecting hazard identification in the industrial sector could violate the Health and Safety at Work Act.
Assuming a single evaluation is enough neglects the need for continuous updates. Hazards evolve with new equipment or processes, so assessments must adapt accordingly. Relying on outdated assessments risks missing emerging dangers.
Conclusion
Understanding the difference between hazard identification and risk assessment is key to improving workplace safety. Hazard identification helps you spot potential dangers, like slippery surfaces or exposed wires, while risk assessment looks at how likely and severe those dangers are. Together, they guide your actions, helping you focus on high-priority risks.
Applying these methods ensures better compliance with safety standards, such as the Health and Safety at Work Act. By combining hazard identification and risk assessment, you reduce workplace accidents and allocate resources effectively. Integrating both processes creates safer conditions and supports long-term safety improvements.
Avoiding challenges like limited resources or confusion between processes is also crucial. Staying proactive helps you address risks as they arise, maintain compliance, and build a safer working environment.
Frequently Asked Questions
What is the difference between hazard identification and risk assessment?
Hazard identification focuses on recognising potential dangers, such as exposed wiring or toxic substances, while risk assessment evaluates how likely and severe the impact of these hazards might be. Together, they form the foundation of workplace safety management.
Why is hazard identification important?
Hazard identification is critical as it serves as the first step in managing workplace risks. It helps pinpoint potential dangers, enabling organisations to address safety concerns proactively and minimise threats to employees.
What are the steps in conducting a risk assessment?
Risk assessment involves identifying hazards, analysing the likelihood and consequences of the risks, and evaluating them against safety standards to prioritise actions for mitigation.
How do hazard identification and risk assessment work together?
Hazard identification highlights potential dangers, while risk assessment evaluates those dangers’ significance. Combined, they ensure a systematic approach to identifying, prioritising, and addressing workplace safety concerns.
What are some common workplace hazards?
Common hazards include unstable shelving, chemical exposures, biological dangers like mould, ergonomic stressors, heavy machinery risks, and falling objects, depending on the industry.
How do industries apply hazard identification and risk assessment differently?
Different industries adapt these practices to their needs. For example, construction prioritises falling objects, healthcare focuses on biohazards, and manufacturing examines machine-related safety concerns.
What are the benefits of combining hazard identification and risk assessment?
Integrating both methods enhances decision-making, ensures effective resource allocation, reduces workplace accidents, and improves compliance with safety standards like the Health and Safety at Work Act 2015.
What challenges are associated with risk assessments and hazard identification?
Challenges include resource constraints, procedural misunderstandings, human errors, and inconsistent data collection, which can compromise accuracy and effectiveness.
How can organisations ensure effective hazard and risk management?
Organisations can involve employees, provide proper training, continuously update safety assessments, allocate resources wisely, and follow regulatory standards to ensure effective management.
Why is regulatory compliance important in hazard and risk evaluations?
Compliance with regulations like the Health and Safety at Work Act ensures organisations meet legal safety obligations, reduce risks, and promote a secure work environment.